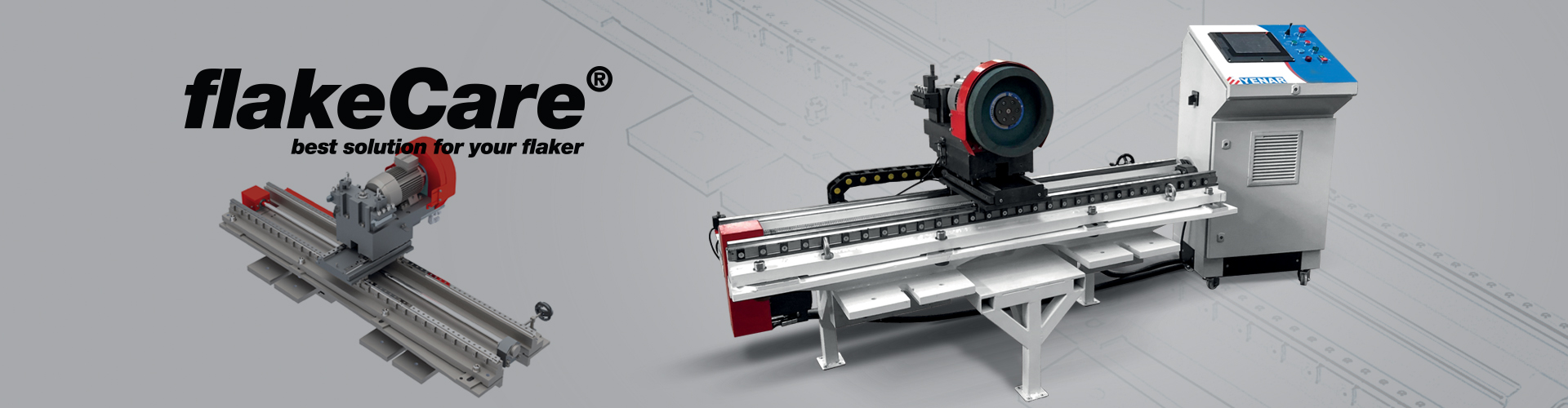
Best Solution For Your Flaker
YMTG Yenar Mobile Turning and Grinding Machine
Yenar's flaking roll turning and grinding unit flakeCare allows you to refurbish the flaking roll surface in your flaking mill on site without the rolls. It is a robust and easy to install CNC mobile machine designed to keep the rollers of your flaking machine in perfect condition every time.
Regular maintenance of the surface of flaking rolls is a necessary preventive action to extend the life of the rolls. Yenar Mobile Turning and Grinding unit firstly the surfaces which allows you to finish the operation faster and in a shorter time compared to other similar machines in the markets and then clear the surface by grinding process. This combined unit is designed especially for 600 mm and 800 mm diameter rolls. Only need to fix it to your flaking mill and operate it according to your roll condition.
Regular maintenance of the surface of flaking rolls is a necessary preventive action to extend the life of the rolls. Yenar Mobile Turning and Grinding unit firstly the surfaces which allows you to finish the operation faster and in a shorter time compared to other similar machines in the markets and then clear the surface by grinding process. This combined unit is designed especially for 600 mm and 800 mm diameter rolls. Only need to fix it to your flaking mill and operate it according to your roll condition.
Specifications
Diameter
600 mm - 820 mm
600 mm - 820 mm
Length
Up to 2.200 mm
Up to 2.200 mm
Total Power
3,7 Kw
3,7 Kw
Power Supply
400 V / 50 Hz
400 V / 50 Hz
Weight (Approx.)
800 kg
800 kg
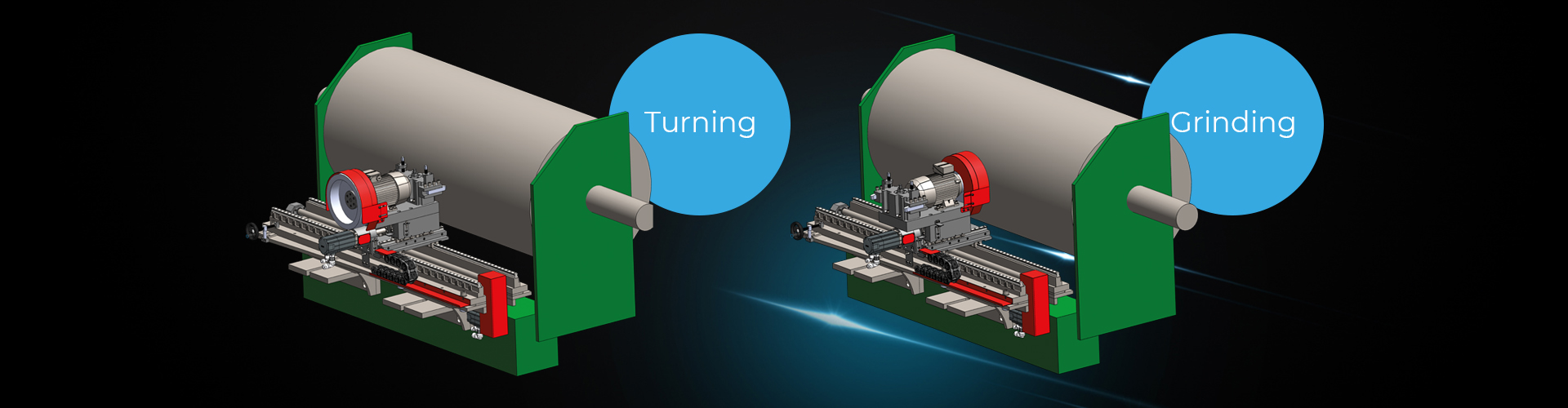
Some Top Problems On The Flaking Rolls
1. Surface of the flaker rolls not only wearing out regularly also sometimes cracking because rolls are touching each other and chips of the material are split out.
2. Sometimes due to wrong feeding or different hydraulically pressure can cause the conical wear on the rolls.
3. As we mentioned above, rolls are touching each other and this cause to getting bigger on the both ends of the rolls compare to middle like wire effect. In this case you should make a chamfer on both ends and machine is CNC controlled that’s why you can make automatically chamfer only need to input chamfer length and depth such generally ( 150 mm length and 0,2 mm depth).
4. By the way refurbishment process of these rolls are very long time.
2. Sometimes due to wrong feeding or different hydraulically pressure can cause the conical wear on the rolls.
3. As we mentioned above, rolls are touching each other and this cause to getting bigger on the both ends of the rolls compare to middle like wire effect. In this case you should make a chamfer on both ends and machine is CNC controlled that’s why you can make automatically chamfer only need to input chamfer length and depth such generally ( 150 mm length and 0,2 mm depth).
4. By the way refurbishment process of these rolls are very long time.
Flaking Rolls Maintenance
Normal Wearing Rolls
This figure never happens in reality.

Wire Effect
Rolls can be as shown photo due the below reasons.
- If the load in the center too high a wire effect makes the roll breaks in the center.
- Due feeder misaligned or bad knives cleaning
- If the load in the center too high a wire effect makes the roll breaks in the center.
- Due feeder misaligned or bad knives cleaning

Polygon Effect
Polygon shape generated along the axis of the roll. This scatter marks are typical for all rolls with differential speed.

Conical Wear
Sometimes due to wrong feeding or different hydraulically pressure can cause the conical wear on the rolls.

Breaking Ending
Surface and two ends of the flaker rolls not only wearing out regularly also sometimes cracking because rolls are touching each other and chips of the material are split out.

Chamfer
Automatically making Chamfer is available.

© 2020 YENAR